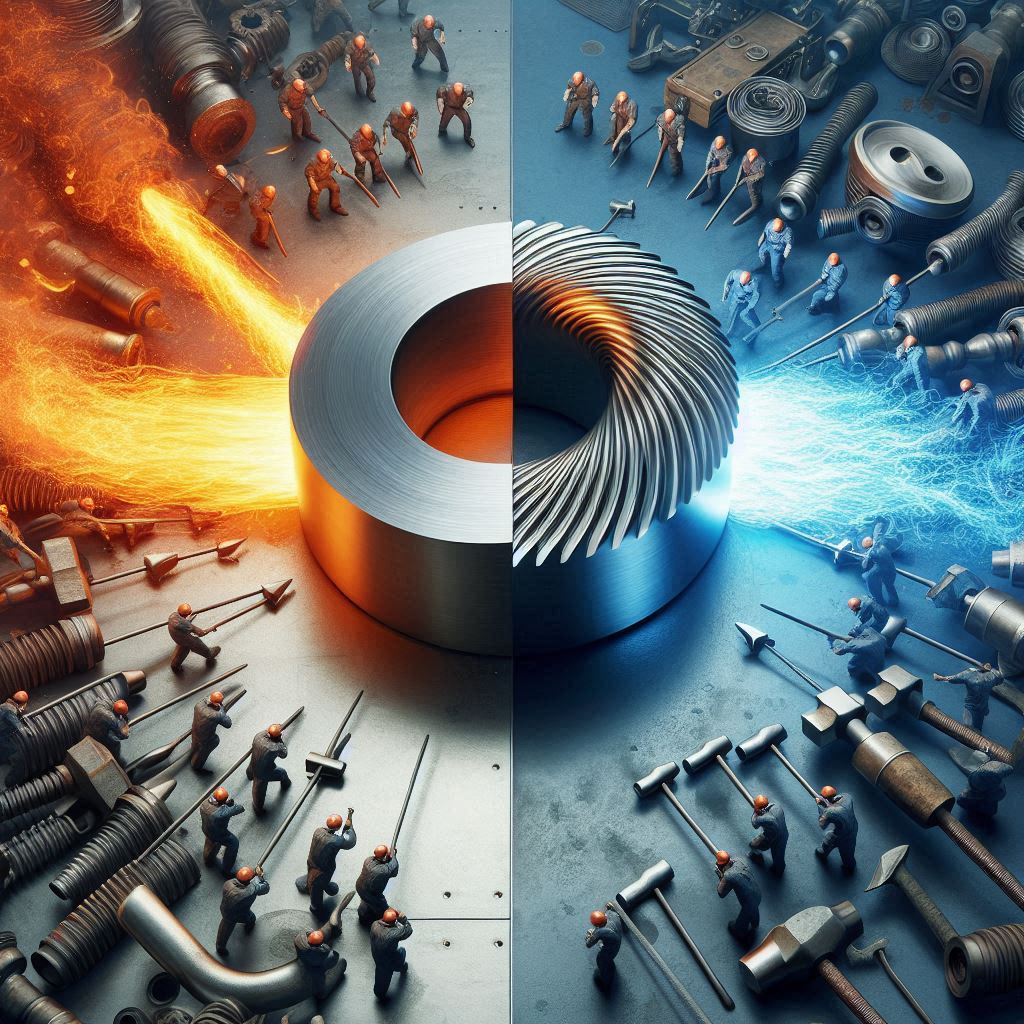
Cold Heading vs. Forging: Key Differences and Applications
Manufacturing metal parts need smart choices about production methods. You want to know which process fits your needs best. The cold forging process creates strong parts that last long. The metal forming industry keeps growing with new techniques.
Cold heading vs forging process differences matters greatly when planning metal part production. At RPPL Industries Ltd, many clients are confused between cold heading and forging. You need to pick the right method for your metal parts. Each process has its own benefits for different projects. The difference between hot forging and cold forging shows in the final product quality.
What is Cold Heading?
Cold heading shapes metal at room temperature. You start with wire or rod material. The process pushes metal into dies to form specific shapes. This works well for making fasteners and small parts.
The metal flows into the shape you want without heating. You can make complex shapes in one step. The process runs faster than many other methods. The cold heading gives you very precise parts.
Your parts come out stronger because of work hardening. The grain structure improves during forming. You waste less material with this process. The surface finish looks better than hot-formed parts.Cold heading applications in manufacturing range from fasteners to precision components.
What is Forging?
Advantages of cold forging include better strength and less waste. You heat metal until it becomes soft and shape able. The process uses hammers or presses to shape the hot metal.
Forging creates very strong parts through controlled deformation. You can make larger parts than with cold heading. The process works with many different metals. Forged parts handle high stress well.
Your parts get consistent properties throughout their structure. The grain flow improves part strength. Forging suits both small and large production runs.
Understanding Key Differences
These methods serve different needs in metal forming. Forging vs cold heading for metal parts shows distinct advantages in various situations. Your choice affects cost quality and production speed.
Benefits of cold heading vs forging in metalworking include faster production and better precision. Let’s explore the main differences between these processes.
Production Speed and Output
Cold heading runs faster than forging operations. You get more parts per hour with cold heading. The automated process needs less operator input. Cold heading machines make thousands of parts hourly. Your production planning becomes easier with steady output rates.
Size and Shape Limitations
Forging handles larger parts than cold heading can manage. You face fewer size restrictions with forging. Cold heading works best for smaller precision parts. Each method suits different product types.
Your design options change based on the chosen process. Forging allows more complex shapes in larger sizes. Cold heading excels at making small and detailed parts.
Cost Considerations
Cold heading saves money on high-volume productions. You use less material than with forging. The faster process reduces labour costs. Energy costs stay lower without heating metal.
Your project budget stretches further with efficient processes. RPPL Industries Ltd. helps clients understand cost differences.
Your manufacturing success depends on picking the right metal forming method. Also, when to use cold heading vs forging for production depends on your specific requirements.
Cold heading and forging each have clear advantages. The choice affects your product quality and costs. Think about size, production volume, and material needs.
Choose based on your specific requirements and goals. Contact Cold Headed Parts expert who know both processes well. They help you make informed manufacturing decisions.